Raise Your Manufacturing Quality with State-of-the-Art Metal Stamping Services
Discovering the World of Metal Stamping: From Design to Production
Within the world of production, steel marking stands out as an accurate and effective approach for forming steel sheets right into numerous forms with remarkable consistency. From the preliminary style phase where complex patterns form to the detailed manufacturing procedures, steel marking is a mix of virtuosity and design. Looking into this globe introduces an intricate interplay of imagination and technological mastery, providing a glimpse right into a realm where innovation meets craftsmanship.
History of Metal Stamping
Steel marking, an extensively made use of production procedure today, has a rich history that dates back to old times (Metal Stamping). The beginnings of steel stamping can be traced to old human beings such as the Egyptians, that made use of stamping methods to adorn jewelry and accessories with complex styles. In time, metal marking progressed, with people like the Greeks and Romans utilizing it for creating coins and attractive products
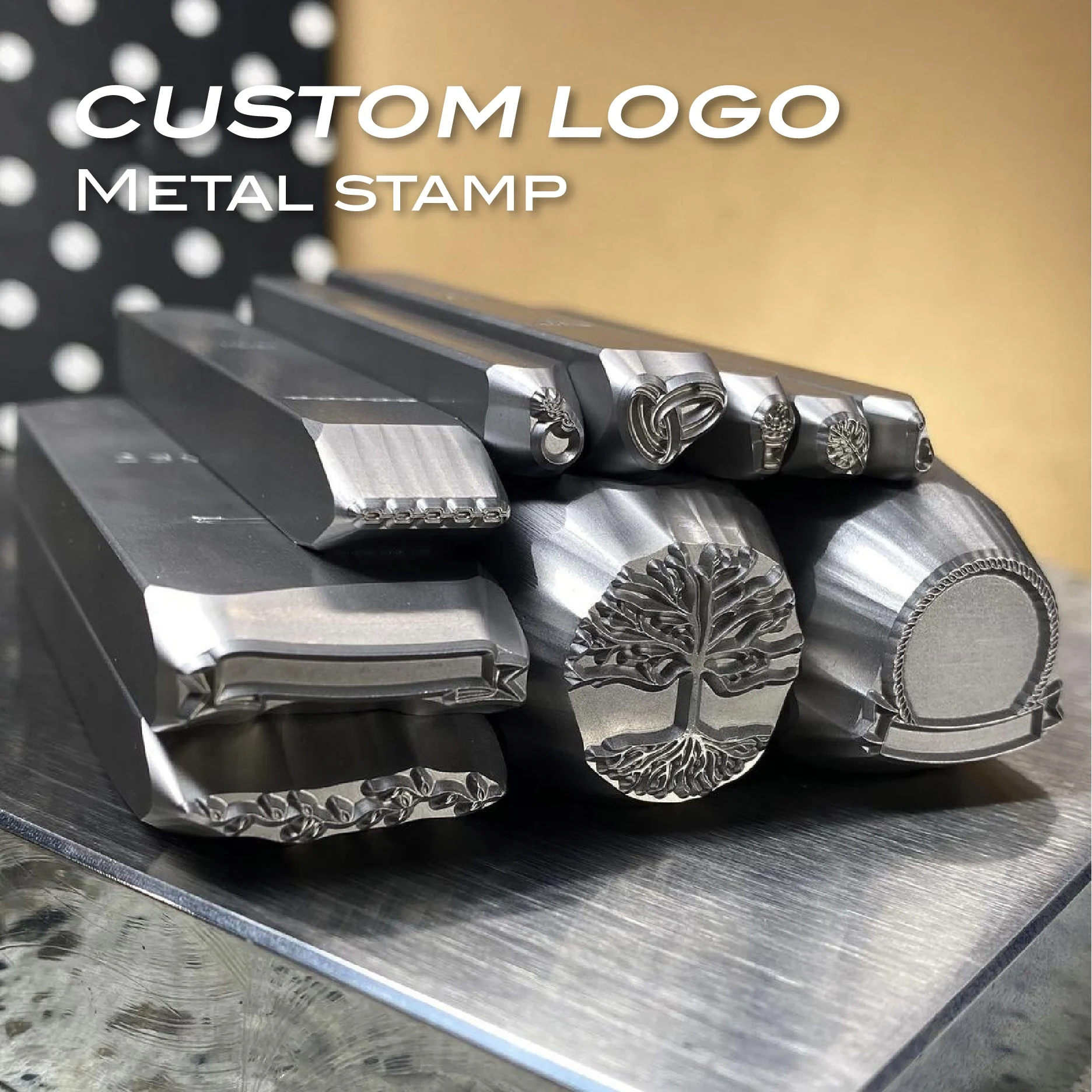
In the 20th century, metal marking continued to evolve with the assimilation of automation and computer system numerical control (CNC) technology. These advancements better enhanced the efficiency and accuracy of metal marking procedures, making it a vital part of modern production across sectors such as auto, aerospace, and electronic devices. Today, metal stamping continues to be an essential manufacturing process, incorporating custom with innovation to fulfill the demands of a constantly progressing market.
Design Considerations and Prototyping
Style considerations in metal stamping include material selection, part geometry, tooling design, and manufacturing expediency. Tooling design plays a substantial role in the success of metal marking tasks, influencing component accuracy, device long life, and production performance.
Prototyping is a crucial stage in the steel stamping procedure that enables engineers to examine the style, validate manufacturability, and make essential modifications prior to full-blown production. By meticulously taking into consideration style aspects and using prototyping, producers can simplify the metal marking process and attain top notch, cost-effective manufacturing outcomes.
Tooling and Tools Fundamentals
Taking into consideration the important this role that tooling layout plays in the success of metal marking tasks, comprehending the essential devices and tools needed is paramount for accomplishing reliable production outcomes. Tooling is a basic element of steel marking, as it straight affects the top quality and uniformity of the last products. Necessary devices include passes away, punches, and components, which are custom-made to shape and create the metal right into the desired components. Dies are the primary tool utilized to reduce and form the metal, while strikes assist develop openings or particular shapes. Components hold the steel in position during the stamping process, making certain precision and repeatability. Additionally, devices such as marking presses, feeders, and coil handling systems are critical for automating the marking process and increasing performance. Purchasing high-quality tooling and equipment not only enhances manufacturing performance yet additionally leads to higher precision, decreased waste, and general expense savings in metal click here to find out more stamping operations.
Manufacturing Refine and Quality Assurance
Efficiently taking care of the manufacturing process and implementing durable quality assurance steps are important for ensuring the success of steel stamping tasks. The manufacturing process in steel stamping entails a collection of steps that have to be very carefully collaborated to achieve ideal results. It starts with the preparation of resources, complied with by the setup of the marking devices and tooling. Operators after that feed the materials right into journalism, where the stamping procedure takes place. Throughout this procedure, it is essential to monitor the manufacturing line for any type of concerns that may influence the high quality of the stamped components.
Quality control in metal stamping is vital to supply products that meet the needed specs. Evaluating the stamped components at various stages of production assists determine any type of issues early on, preventing costly additional reading rework or scrap. Methods such as dimensional assessment, aesthetic examination, and product screening are generally used to ensure the top quality of the stamped parts. By preserving rigorous top quality control standards, manufacturers can support their reputation for delivering premium metal stamped items.
Applications and Sector Insights
In the realm of metal marking, the effective application of production processes and high quality control procedures straight affects the efficiency and reliability of different market applications and supplies beneficial insights into the industry's operational dynamics. Furthermore, steel marking assists in the manufacturing of numerous house appliances, including refrigerators, cleaning equipments, and stoves, by providing economical options for producing long lasting and complicated parts. Comprehending the applications and market understandings of steel marking is crucial for maximizing manufacturing procedures and improving product quality across various sectors.

Final Thought
Design factors to consider, prototyping, tooling, equipment, production procedures, and quality control are essential elements of metal marking. With its widespread applications and market insights, metal marking continues to be a flexible and efficient manufacturing procedure.